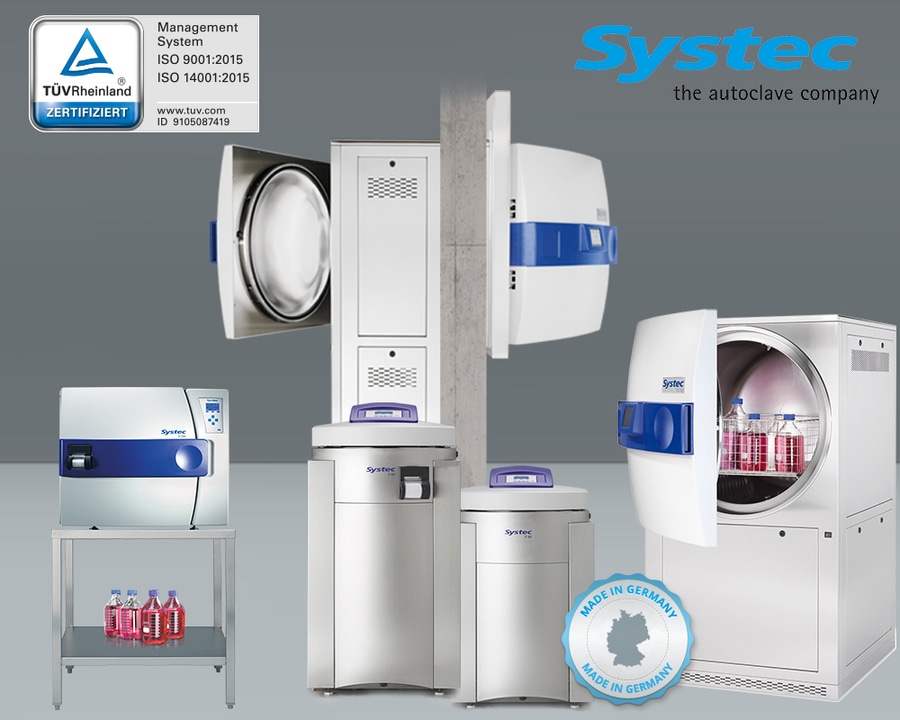
Automatische Übersetzung anzeigen
Dies ist eine automatisch generierte Übersetzung. Wenn Sie auf den englischen Originaltext zugreifen möchten, klicken Sie hier
#Produkttrends
{{{sourceTextContent.title}}}
Qualifikation und Bestätigung von Laborautoklaven
{{{sourceTextContent.subTitle}}}
Bestätigung von Autoklaven
{{{sourceTextContent.description}}}
Die Notwendigkeit des Qualifizierens eines Autoklavs und der Validierung des Sterilisationsprozesses ergibt sich aus verschiedenen Gesetzen und Regelungen. Obgleich die Ausdruckqualifikation und -bestätigung normalerweise in Qualification_Validationone-Satz erwähnt werden oder sogar synonym verwendet, werden verschiedene Aussagen und Ansätze hinter ihnen versteckt.
Die Notwendigkeit, zum eines Autoklavs zu qualifizieren und des Sterilisationsprozesses zu validieren kommt von unter anderem die Medizin fungieren, die medizinischen Geräte fungieren, das Chemikaliengesetz und die Verordnung auf dem Schutz von biologischen Substanzen und Gentechnikvon. Diese Gesetze und Regelungen beziehen manchmal sich Richtlinien, Regelungen oder auf Entscheidungen der Kommission, der Richtlinien und der Standards. Durch das Verweisen von rechtsverbindlichen EU-Verordnungen auf erlaubterweise nicht-bindene Standards oder von Richtlinien wie die Eu--GxPrichtlinien für
Gute Herstellungsmethode (GMP)
Gute klinische Praxis (GCP)
Gute Laborpraxis (GLP)
sie werden einen Gesetz ähnlichen Charakter gegeben und ihre Befolgung wird überprüft und gesteuert regelmäßig durch Regierungsagenturen. Das Ziel ist sicherzustellen und garantiert einem hohen und vor allem einheitlichen Qualitätsstandard. Wie die einzelnen Regelungen und einander differenziert zwischen werden, wird im Abbildung 1. gezeigt
Entsprechend den Eu--GxPrichtlinien Systeme und Prozesse, die direkt in das Herstellungsverfahren für Produktgruppen wie pharmazeutische Produkte, Wirkstoffe, Kosmetik, Nahrung-, Tierfutter und medizinische Geräte und folglich miteinbezogen, einen Einfluss auf Produktqualität müssen qualifiziert werden und validiert werden haben werden. Die Anforderungen des Führers zur guten Laborpraxis werden an den Labors angesprochen, die nicht-klinische Untersuchungen über Testobjekte wie pharmazeutische Produkte, Schädlingsbekämpfungsmittel, Biozide, Kosmetik, Tierarzneimittel, Lebensmittelzusatzstoffe, Zufuhrzusätze und industrielle Chemikalien leiten. Die Systeme und Prozesse, die verwendet werden, um menschliche Beispielmaterialien (Körperflüssigkeiten, Gewebe, Zellkulturen, etc.) zu inaktivieren, Mikroorganismen, Zellkulturen, Endoparasites – einschließlich ihre genetisch geänderten Formen – fallen auch unter diese Kategorie.
Eine Anforderung der Prinzipien der guten Laborpraxis ist-, dass Ausrüstung, einschließlich die validierten computergestützten Systeme, die benutzt werden, um zu sammeln, Daten zu notieren und zu reproduzieren und die Umweltbedingungen zu steuern relevant sind zum Test, vom ausreichenden Entwurf und von der Leistung sein muss. Wenn Ihr Autoklav direkt in Untersuchungen über die oben erwähnten Produktgruppen miteinbezogen wird, muss seine Eignung im Hinblick auf Entwurf und Leistung nachgewiesen werden. Im Detail definieren die Aufsichtsbehörden die Anforderungen für Qualifikation und Bestätigungsdurchführung möglicherweise und -dokumentation ausführlicher, indem sie Standards, Richtlinien, etc. oder sie spezifizieren, folgen Standards, weil die Standardisierung sich auch innerhalb bestimmter Grenzen bewegt.
Qualifikation und Bestätigung
Als Autoklavbetreiber, der mit Ihrem Herstellungsverfahren beschäftigt gewesen wird – oder als Laborbetreiber – Sie, sind- für Ihr Herstellungsverfahren oder für die Ergebnisse und die Schlussfolgerungen Ihrer Studie verantwortlich. Qualifikation und Bestätigung wird häufig mithilfe eines passend qualifizierten Dienstleisters durchgeführt. Da, nur Sie die Produkt-spezifischen Anforderungen für Ihren Prozess definieren können, ist enge Zusammenarbeit zwischen Ihren Spezialistenabteilungen, der näheren Bestimmung/Validator und dem Autoklavhersteller notwendig.
Obgleich die Ausdruckqualifikation und -bestätigung normalerweise in einem Satz erwähnt werden oder sogar synonym verwendet, werden verschiedene Aussagen und Ansätze hinter ihnen versteckt. Der gemeinsame Nenner beider Konzepte ist, dass Dokumente in Übereinstimmung mit den Richtlinien, die die Definition der einzelnen Tests und die Dokumentation der Testergebnisse enthalten, erstellt werden müssen. In vielen Fällen umfasst die schriftliche Qualifikation/der Bestätigungsplan auch Protokolle, die verwendet werden, um die Testergebnisse während der Durchführung zu dokumentieren.
Qualifikation: Im Rahmen einer Systemqualifikation muss Beweis sein, vorausgesetzt, dass ein System mit der Technologie, die eingesetzt wird, für die beabsichtigte Aufgabe passend ist, tadellos arbeitet und Ergebnisse liefert, die die Bedingungen erfüllen. Der Hauptfokus hier ist deshalb auf dem System (der Autoklav) und seiner korrekten Funktion.
Bestätigung: Das Ziel der Prozessvalidierung ist, zu prüfen, dass der Prozess effektiv ist und ein Produkt (Ergebnis) liefern kann das reproduzierbar ist und den erforderlichen Qualitätsanforderungen genügt. Der Hauptfokus ist deshalb auf dem Prozess selbst und Beweis der Befolgung der Annahmekriterien, die vom Konsol-Operator definiert werden soll.
Die Prozessqualifikation ist häufig ein Prozess, der innerhalb eines Systems stattfindet, das die Verbindung von Ausdrücken erklärt. Die Qualifikation und das Anerkennungsverfahren wird im Abbildung 2. veranschaulicht
DQ – Entwurfs-Qualifikation
Das erste Qualifikationsstadium eines Autoklavs beginnt, sobald Sie Ihre Anforderungen formulieren und dokumentieren, damit das Gerät gekauft werden kann. Dies heißt, dass Sie bereits Ihre Benutzer-Anforderungs-Spezifikation (URS) geschaffen haben; d.h. die Anforderungen, die von einem Gerät gemacht werden und die erfüllt werden müssen. Für viele Hersteller können Autoklaven mit Wahlen zum Beispiel ausgerüstet werden, die Prozessgenauigkeit oder Geschwindigkeit beeinflussen. Wenn bestimmte Wahlen abhängig von den durchgeführt zu werden Prozessen nicht im URS berücksichtigt werden und wenn sie nicht entsprechend dem Gerät verbessert werden, kann diese erfolgreiche Qualifikation und die Bestätigung beträchtlich schwieriger oder sogar vollständig unmöglich später machen. Sogar an diesem Anfangsstadium, sollten zukünftige Betreiber deshalb genau spezifizieren, was der Autoklav verwendet werden soll für, welche Anforderungen auf die Prozesse gesetzt werden sollen, und das Standards und Richtlinien beobachtet werden müssen.
Abhängig von der Komplexität des Systems oder des Autoklavs, unterscheidet sich der Bereich des URS groß. Autoklavlieferanten reichen ein Angebot auf dieser Basis ein und, in der Koordination zwischen dem Betreiber und dem Hersteller, werden Spezifikationen aufgestellt. Die Prüfung auf Übereinstimmung ist eine grundlegende Komponente des ersten Qualifikationsniveaus – die Entwurfs-Qualifikation (DQ). Nach einem erfolgreichen DQ wird das Gerät durch den Hersteller entsprechend den vereinbarten Spezifikationen hergestellt. Gleichzeitig (entweder innerlich, mit dem Hersteller oder mit einem unterschiedlichen Dienstleister), die Dokumente erstellend, die für den folgenden Schritte IQ erfordert werden, können OQ und PQ (Bestätigungsplan) jetzt begonnen werden. Diese Dokumente bilden die Basis für die Implementierung des IQs, OQ und PQ und spezifizieren die Inspektionen und die durchgeführt zu werden Tests, sowie ihre Parameter und Annahmekriterien. Ausführliche Dokumentation wird angefordert, um zu prüfen, dass alle Kontrollen und Tests erfolgreich abgeschlossen worden sind.
IQ – Installations-Qualifikation
Nachdem die Entwurfsqualifikation erfolgreich abgeschlossen worden ist und das Gerät erfolgreich geliefert worden ist, kann das folgende Qualifikationsstadium des Autoklavs auf Standort anfangen – die Installationsqualifikation (IQ). Die Eignung des Installationsstandorts, die körperlichen Eigenschaften des gelieferten Autoklavs sowie die Vollständigkeit der Dokumentation, die dem Gerät gehört, wird jetzt in den Qualifikationsdokumenten überprüft und dokumentiert. Dokumentation umfasst im Allgemeinen die Bedienungsanleitungen, die Wartung, die Reinigung und die Kalibrierungsanweisungen sowie materiellen die Zertifikat- und Leistungsblätter für einzelne installierte Komponenten.
Wenn dieses Qualifikationsniveau auch erfolgreich abgeschlossen worden ist oder wenn sind irgendwelche Abweichungen, die möglicherweise ermittelt worden, aufgrund von einer Risikoanalyse und -geeigneten Maßnahmen ausgewertet worden sind, eingeleitet worden, um sie zu beseitigen, kann die Funktionsqualifikation (OQ) des Systems begonnen werden.
OQ – Betriebsqualifikation
Beweis ist jetzt, vorausgesetzt, dass die Geräte, die Installationen, die Dienstprogramme und die Systeme die Anforderungen und die Spezifikationen des Betreibers treffen, die im Rahmen der Entwurfsqualifikation spezifiziert wurden. Tests werden durchgeführt, um zu prüfen, dass das Gerät entsprechend Plan funktioniert. Dieses schließt Kalibrierung ein sowie simuliert Störung, Störung und Abschaltungszustände des Gerätes. Dieses Verfahren dient als dokumentierter Beweis, den Defekte Sicherheit-relevant sind, die möglicherweise, oder, Qualität-beeinflussend für das Produkt, werden richtig ermittelt durch den Autoklav.
Sterilisationsläufe des Autoklavs ohne eingeführtes Produkt einzuführen ist auch Teil des Bereichs der Funktionsqualifikation. Temperaturfühler und ein Druck-Sensor werden in den Autoklav für dieses eingefügt, die einen Datenlogger benutzen, um Druck und Temperatur unabhängig des Autoklavprüfers zu messen. Die Temperatur- und Druckwerte, die können bestimmt werden gegen die Werte auf diese Art, folglich überprüft werden, die über die Autoklavsteuerung bestimmt werden. Darüber hinaus werden die Bioindikatoren, die auf Bacillus Stearothermophilus basieren, in die Autoklaven eingeführt, um die biologische Wirksamkeit des Sterilisationsprozesses zu prüfen. Das Ziel ist, dokumentierten Beweis zur Verfügung zu stellen, dass ein System oder ein Gerät für seinen beabsichtigten Gebrauch ohne ein Produkt passend ist.
PQ-, Leistungs-Qualifikation
Sobald der Autoklav nachgewiesen worden ist, ohne ein Produkt zu arbeiten, wird die Leistung des Gerätes entsprechend den Spezifikationen des Bestätigungsplanes definierte im Voraus, mit dem Ziel der Prüfung überprüft, dass die spezifizierten Prozessanforderungen ausreichend unter wirklichen Bedingungen genügt werden (mit einem Produkt). Es sollte gemerkt werden, dass die Temperaturverteilung vom entkeimt zu werden abhängt Produkt, und deshalb ein unterschiedlicher PQ-Test für jede ladende Konfiguration durchgeführt werden muss. Ladenmuster werden für dieses definiert, das Vertreter der in der täglichen Operation erwartet zu werden Lasten sein sollte. Dieses wird häufig entsprechend dem folgenden Entwurf getan:
Minimales Laden,
Mittleres Laden,
Laden des schlimmsten Falls.
Der schlimmste Fall, der absolut lädt, muss hinsichtlich der ladenden Quantität überprüft werden, zum Beispiel. Andere Parameter müssen möglicherweise betrachtet werden, wenn sie das Ergebnis des Sterilisationsprozesses beeinflussen konnten.
Wie mit dem OQ, wird der Sterilisationsprozeß durch Temperatur- und Druck-Sensoren überprüft, die die entsprechenden Daten unabhängig der Autoklavsteuerung mittels eines Datenloggers notieren. Darüber hinaus wird die biologische Wirksamkeit des Sterilisationsprozesses auch durch die Bezugsindikatoren gezeigt, die auf Bazillus sterothermophilus basieren. Im PQ anders als im OQ, werden die Temperaturfühler sowie die Bioindikatoren in das geprüft zu werden gelegt Produkt, (ladendes Muster) um Beweis der Sterilisierungswirksamkeit im Produkt zur Verfügung zu stellen. Es ist wichtig, dass die Temperaturfühler sowie die Bioindikatoren in die Punkte des Produktes gelegt werden, in dem es erwartet wird, dass ein Sterilisierungseffekt am schwierigsten zu erzielen ist. Das Ziel ist dokumentierter Beweis, dass ein Prozess das erwartete Ergebnis reproduzierbar liefern kann, welches das Produkt berücksichtigt.
Wenn sie das OQ und das PQ durchführt, sollte die Anzahl von Temperaturmessungspunkten innerhalb der Arbeitskammer mit den Empfehlungen der relevanten Standards wie en 556 oder der GxP-Richtlinien übereinstimmen, da jede mögliche Abweichung von diesen vermutlich zu Fragen während einer Inspektion führt. 12 messende Punkte der Temperatur sollten pro 1 m3 der Sterilisationskammer deshalb zur Verfügung gestellt werden. Ein Bioindikator, der auf dem Bacillus Stearothermophilus basiert, wird an jedem messenden Punkt der Temperatur gesetzt.
Sterilitäts-Versicherungs-Niveau
Der Standard en 556 stellt auch Informationen auf, wenn ein Produkt beschrieben werden kann, wie steril, oder wenn einem Sterilisationsprozeß als reproduzierbar gilt, d.h. liefert immer das gleiche Ergebnis zur Verfügung (ein steriles Produkt). Was genannt wird, wird das Sterilitäts-Versicherungs-Niveau (SALZ) hier definiert. Das SALZ nimmt eine theoretische Bevölkerung von 100 000 (105) Mikroorganismen (Kolonienbildungs-Einheiten – CFU), zum Beispiel an.
Bacillus Stearothermophilus wird als Bezugsindikator (Bioindikator) für Prüfungsdampfsterilisationsprozesse benutzt. Das SALZ verlangt jetzt, dass, abhängig von dem entkeimt zu werden Produkt, die größte mögliche Wahrscheinlichkeit erzielt werden muss, dass alle Mikroorganismen wirklich getötet werden und folglich alle Produkte wirklich steril sind. Diese größte mögliche Wahrscheinlichkeit gilt als nachgewiesen, wenn ein SALZ-Wert von 10-6 erreicht wird. Dies heißt dass die Wahrscheinlichkeit, dass ein Produkt noch nicht steril ist, nachdem der Sterilisationsprozeß 1: 1 000 000 ist.
Wieder-Bestätigung
Wenn alle Qualifikationsschritte und die Prozessvalidierung erfolgreich abgeschlossen worden sind, muss der Betreiber einen Abstand für Wiederbestätigung spezifizieren. Es ist eine gute Idee, mit dem Autoklavhersteller an diesem Punkt zu koordinieren, da es sinnvoll ist, die Wiederbestätigung mit der notwendigen wiederkehrenden Kalibrierung der Instrument-Sensoren zu kombinieren.
Vorsicht wird angefordert, wenn man Prozessparameter ändert. Dieses schließt, zum Beispiel ein
Ändernde Gerätparameter (z.B. ändernde Sterilisationstemperatur und/oder -zeit);
Änderungen in der ladenden Konfiguration oder Änderungen in der Zusammensetzung des entkeimt zu werden Produktes,
Änderungen beim Verpacken für verpackte Waren,
Reparaturen an der Ausrüstung und am verbundenen Ersatz von Komponenten,
Gerätsoftware-aktualisierungen.
Wenn die oben erwähnten Änderungen eintreten, muss ihr Einfluss auf den validierten Gesamtprozeß überprüft werden. Wenn es erwartet werden soll, dass die Änderung einen Einfluss auf den Gesamtprozeß haben könnte, muss der Einfluss als Teil der Wiederbestätigung bestimmt werden, ausgewertet werden und dokumentiert werden. Dieses ergibt möglicherweise notwendige Anpassungen zum Gesamtprozeß, damit es fortfahren kann, mit den Parametern übereinzustimmen, die vor der Änderung definiert werden.
Da Änderungen auch allmählich eintreten können, d.h. kaum oder sogar überhaupt nicht merklich, sollte Wiederbestätigung in örtlich festgelegten Abständen immer durchgeführt werden. Ein Abstand von einem Jahr ist hier nachgewiesen worden. Für besonders kritische Prozesse jedoch kann der Abstand für Wiederbestätigung in kürzeren Abständen auch definiert werden.