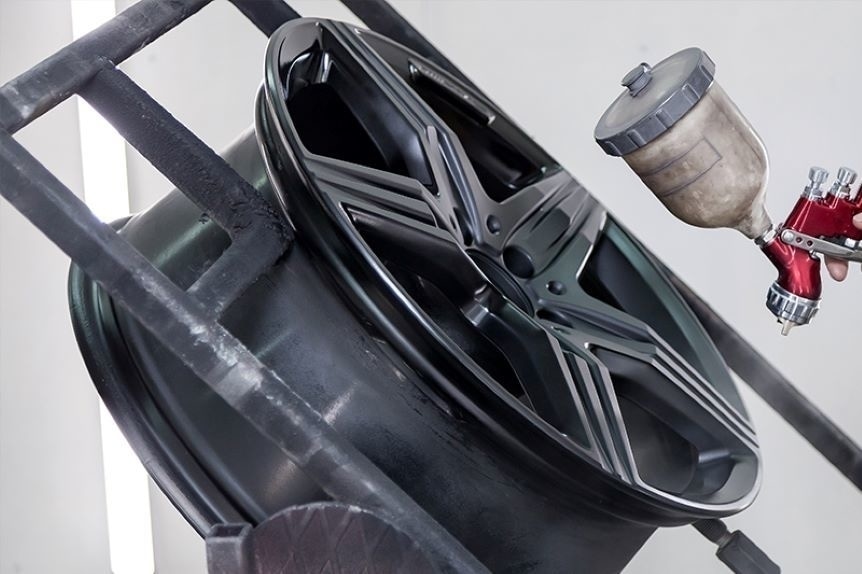
Automatische Übersetzung anzeigen
Dies ist eine automatisch generierte Übersetzung. Wenn Sie auf den englischen Originaltext zugreifen möchten, klicken Sie hier
#Neues aus der Industrie
{{{sourceTextContent.title}}}
Herstellung von Leichtmetallrädern: die Bedeutung der Lackierung
{{{sourceTextContent.subTitle}}}
Überwachung der Temperatur
{{{sourceTextContent.description}}}
In der faszinierenden Welt der Automobilindustrie, in der Leistung auf Eleganz trifft, ist die Herstellung von Leichtmetallrädern ein entscheidendes Kapitel. Dieser anspruchsvolle Prozess, der Technik und Design miteinander verbindet, erfordert in jeder Phase eine sorgfältige Bearbeitung. In den folgenden Abschnitten werden wir die Facetten dieses Prozesses erkunden, von der Auswahl der Materialien bis zur Endbearbeitung und Lackierung, die diesem wichtigen Autozubehör Haltbarkeit und Schönheit verleihen.
Auswahl der Materialien
Einmal montierte Leichtmetallräder sind hohen Belastungen ausgesetzt. Daher ist die Wahl der richtigen Werkstoffe für ihre Konstruktion der wichtigste Schritt, um die Qualität der Leistung des Endprodukts zu gewährleisten.
Ein Leichtmetallrad besteht, wie der Name schon sagt, aus einer Legierung aus verschiedenen Metallen. Die Auswahl und das Verhältnis dieser Werkstoffe beruhen auf den Erfahrungen, die das herstellende Unternehmen im Laufe der Zeit gesammelt hat, und können sich im Laufe der Zeit je nach den Bedürfnissen des Marktes und den neuesten technologischen Innovationen ändern.
Von allen Metallen wird Aluminium bei den meisten heute auf dem Markt befindlichen Leichtmetallrädern am häufigsten verwendet. Seine Beliebtheit ist auf seine Leichtigkeit und einfache Verarbeitung zurückzuführen. Dieses Element wird nie in Reinform verwendet, sondern mit anderen Metallen gemischt, um seine mechanischen Eigenschaften zu verbessern.
Für hochwertige oder wettbewerbsfähige Leichtmetallräder werden häufig Magnesiumlegierungen verwendet. Durch die Verwendung dieses Metalls ist es möglich, Felgen zu erhalten, die genauso stoß- und vibrationsfest sind, aber bis zu 35 Prozent leichter als ihre Pendants aus Aluminium.
Fusion
Nach der Auswahl der Werkstoffe geht es an das Gießverfahren, bei dem die Metalllegierung für die Herstellung der Felgen entsteht.
Das Schmelzen findet in einem speziellen Schmelzofen bei Temperaturen von bis zu 1000 Grad Celsius statt. Die Hersteller verfolgen diese Phase sehr genau und kontrollieren die Zusammensetzung der Legierung mit Hilfe einer optischen Emissionsspektralanalyse. Diese Kontrolle ermöglicht es, die genauen Mengen der verschiedenen geschmolzenen Elemente in der Legierung zu ermitteln.
Wenn alles in Ordnung ist, wird die Metalllegierung in die Felgenform gegossen. Hier wird das Material abgekühlt und gepresst, um die Form vollständig auszufüllen.
Schmieden
Das Schmieden ist ein alternatives Verfahren zum Gießen, das von Herstellern angewandt wird, die hochwertige Produkte anbieten wollen. Es gewährleistet eine gleichmäßige Verteilung der physikalischen Eigenschaften der Felge und vermeidet Inhomogenitäten zwischen den verschiedenen Zonen. Eine geschmiedete Felge reagiert deutlich besser auf Belastungen und Stöße und weist daher auch ein geringeres Risiko der Verformung auf. Ein weiterer Vorteil ist die höhere Festigkeit bei gleichem Materialeinsatz. Dank dieser Eigenschaften können geschmiedete Felgen dünn und leicht sein.
Die Schmiedekosten sind höher als die Gusskosten. Dies liegt zum einen an dem aufwändigen Verfahren und zum anderen an dem hohen Materialabfall bei der Herstellung.
Der Schmiedeprozess beginnt mit dem Schmelzen des Materials, das dann in einer runden Scheibe einem sehr hohen Druck ausgesetzt wird. Anschließend wird die Scheibe durch eine Reihe von Pressungen und Erhitzungen zu einer Felge geformt, bis sie die für das jeweilige Modell vorgesehene Form erreicht hat.
Endbearbeitung
Die Endbearbeitung ist wichtig, um nicht nur die Funktionalität, sondern auch die Ästhetik des Leichtmetallrads zu gewährleisten. Diese Phase umfasst verschiedene Behandlungen, darunter:
rektifikation, d.h. die Korrektur von Asymmetrien und Unvollkommenheiten
beseitigung von Flecken
Die Herstellung des Mittellochs
Eloxierung, die die Felge korrosionsbeständiger macht und ihre ästhetische Wirkung verbessert
Diese Arbeiten lassen sich nicht einfach automatisieren, sondern erfordern die Erfahrung und das Fachwissen von Fachkräften.
Nach der Fertigstellung wird der Staub entfernt, um die Gleichmäßigkeit und Sauberkeit der Felgenoberfläche zu gewährleisten.
Der Produktionsprozess wird mit der letzten Stufe fortgesetzt.
Lackierung
Die Lackierung von Leichtmetallrädern ist, anders als man meinen könnte, eine komplexe und heikle Tätigkeit. Um ein hervorragendes Ergebnis zu erzielen, ist es wichtig, alle Phasen des Prozesses unter Kontrolle zu halten.
Die am häufigsten verwendete Technik ist die Pulverbeschichtung. Bei diesem Verfahren wird ein feines Farbpulver auf die Oberfläche der Felgen aufgetragen und anschließend in einem Lackierofen erhitzt. Durch die Hitzeeinwirkung verflüssigt sich das Pulver und bedeckt die Felge gleichmäßig.
Ein wichtiger Aspekt des Beschichtungsprozesses ist der richtige Umgang mit den hohen Temperaturen. Genaue Überwachung und Kontrolle sind entscheidend, um eine dauerhafte und homogene Beschichtung zu gewährleisten. Suboptimale Temperaturen können Defekte und Unebenheiten in der Beschichtung verursachen, die sowohl die Ästhetik als auch die Funktionalität der Felge beeinträchtigen.
In diesem Zusammenhang hat Tecnosoft eine innovative Lösung eingeführt, die eine angemessene Überwachung der hohen Temperaturen während der Lackierung gewährleistet.
Wie bei vielen unserer Produkte begann alles mit einer sehr spezifischen Anfrage eines Kunden.
Temperaturüberwachung bei der Lackierung von Leichtmetallrädern
Ein bekanntes Unternehmen, das Autoräder herstellt, sah sich mit einer anspruchsvollen Herausforderung konfrontiert. Sein Ziel war es, einen Lackierprozess zu überwachen, um sicherzustellen, dass jede Felge nicht nur ästhetisch einwandfrei, sondern auch außergewöhnlich haltbar ist.
Die Lackierung in Industrieöfen erfordert sehr genaue Temperaturen und Zeiten, so dass eine ständige Überwachung notwendig ist.
Dies ist der Temperaturzyklus, den das Unternehmen für die Lackierung seiner Leichtmetallräder verwendet:
Die erste Phase findet in einem ersten, auf 250 °C aufgeheizten Ofen statt, in dem die Kreise 15 Minuten lang verbleiben.
Danach folgt eine Zwischenphase, in der die Temperatur für 30 Minuten auf 25°C gesenkt wird.
Der Kreis kommt in den zweiten, auf 250 °C aufgeheizten Ofen. Diesmal für einen längeren Zeitraum, 45 Minuten.
Eine zweite 40-minütige Zwischenstufe bei 100°C, gefolgt von einer dritten 30-minütigen Zwischenstufe bei 25-30°C.
Die Felge kommt dann für 35 Minuten in einen dritten Ofen bei 250 °C.
Schließlich folgt die Abkühlungsphase.
Um die Temperatur zu überwachen, mussten also Messgeräte gefunden werden, die sehr hohe Temperaturen über relativ lange Zeiträume aushalten. Eine technologische Herausforderung, die wir Schritt für Schritt in Angriff genommen haben.
Phase 1: Die Vorstudie
Unser Ziel war es, ein Überwachungssystem zu entwickeln, das der Hitze standhält und während der Lackierung genaue Temperaturdaten an verschiedenen Stellen der Felge liefert.
Daher konzentrierte sich die Machbarkeitsstudie auf die Überprüfung der Leistung des TC-Log 8 S USB-Thermoelement-Systems unter den für Lackieröfen typischen hohen Temperaturen.
In dieser Phase prüften wir die verfügbaren Wärmeschutzvorrichtungen für Thermoelemente, stellten aber fest, dass diese nicht für den gesamten Lackierprozess geeignet waren, da sie nur bis zur Hälfte des Erhitzungsprozesses standhalten konnten.
Daher musste eine maßgeschneiderte Lösung gefunden werden, die für diesen Zweck geeignet war.
Schritt 2: Lösungen schaffen
Um diese Einschränkung zu überwinden, änderten wir das äußere Metallgehäuse des bestehenden Wärmeschutzes und ersetzten das innere Material durch eine stärkere Verbindung.
Um die Ausbreitung von Staub zu verhindern, der die Lackierung beeinträchtigen könnte, haben wir das neue Material mit einer geeigneten Beschichtung versehen.
Um die Wärmedämmung zu verbessern und das Eindringen von Wärme so weit wie möglich zu verzögern, haben wir außerdem zwei kleine Metalltanks mit Wasser und einem Entlüftungsventil eingebaut.
Unser Prototyp war also zum Vorschein gekommen!
Phase 3: Der letzte Test
Sobald der Prototyp zur Verfügung stand, unterzogen wir ihn demselben Wärmezyklus, den der Kunde verlangt hatte.
Das Ergebnis war sehr positiv: Der Thermotest wurde mit Bravour bestanden. Das Gerät war in der Lage, Temperaturen von 250° über einen längeren Zeitraum zu überwachen und dabei eine weitgehend zufriedenstellende Sicherheitsmarge aufrechtzuerhalten.
Herausforderungen gemeistert:
Bei der Entwicklung unseres Thermoelement-Systems zur Überwachung von Temperaturen in Lackierprozessen haben wir zwei Herausforderungen gemeistert:
Die erste und schwierigste war die komplette Neukonzeption des Wärmeschutzes. Dabei handelte es sich nicht um eine einfache Überholung, sondern um die Schaffung einer völlig neuen Lösung, die den spezifischen Anforderungen des Hochtemperatur-Lackierprozesses Rechnung trägt.
Parallel dazu haben wir auch das Elektronikgehäuse neu gestaltet. Dieser Schritt war entscheidend, um sicherzustellen, dass das System nicht nur den hohen Temperaturen standhält, sondern auch unter diesen extremen Bedingungen funktionsfähig und zuverlässig bleibt. Wir haben daher erfolgreich eine neue Isolierung getestet, die einen besseren Wärmeschutz bietet, ohne die Funktionalität des Systems zu beeinträchtigen.
Die nächste Herausforderung
Für die nahe Zukunft untersuchen wir eine externe Box, die den Wärmeschutz des Datenloggers enthalten kann.
Ziel ist es, das System in 100 Prozent der Kundenprojekte nutzbar zu machen - ein ehrgeiziges Ziel, das weitere Innovationen und Experimente erfordert.
Diese überwundenen und zukünftigen Herausforderungen zeigen unser ständiges Bestreben, maßgeschneiderte Lösungen anzubieten, die die spezifischen Bedürfnisse unserer Kunden effektiv und genau erfüllen.
Seit 35 Jahren bauen wir unser Know-how aus und festigen so unsere Position als führendes Unternehmen im Bereich der Überwachung komplexer Industrieprozesse.
Kontaktieren Sie uns!